Enhancing Business Efficiency with Injection Moulding Tools
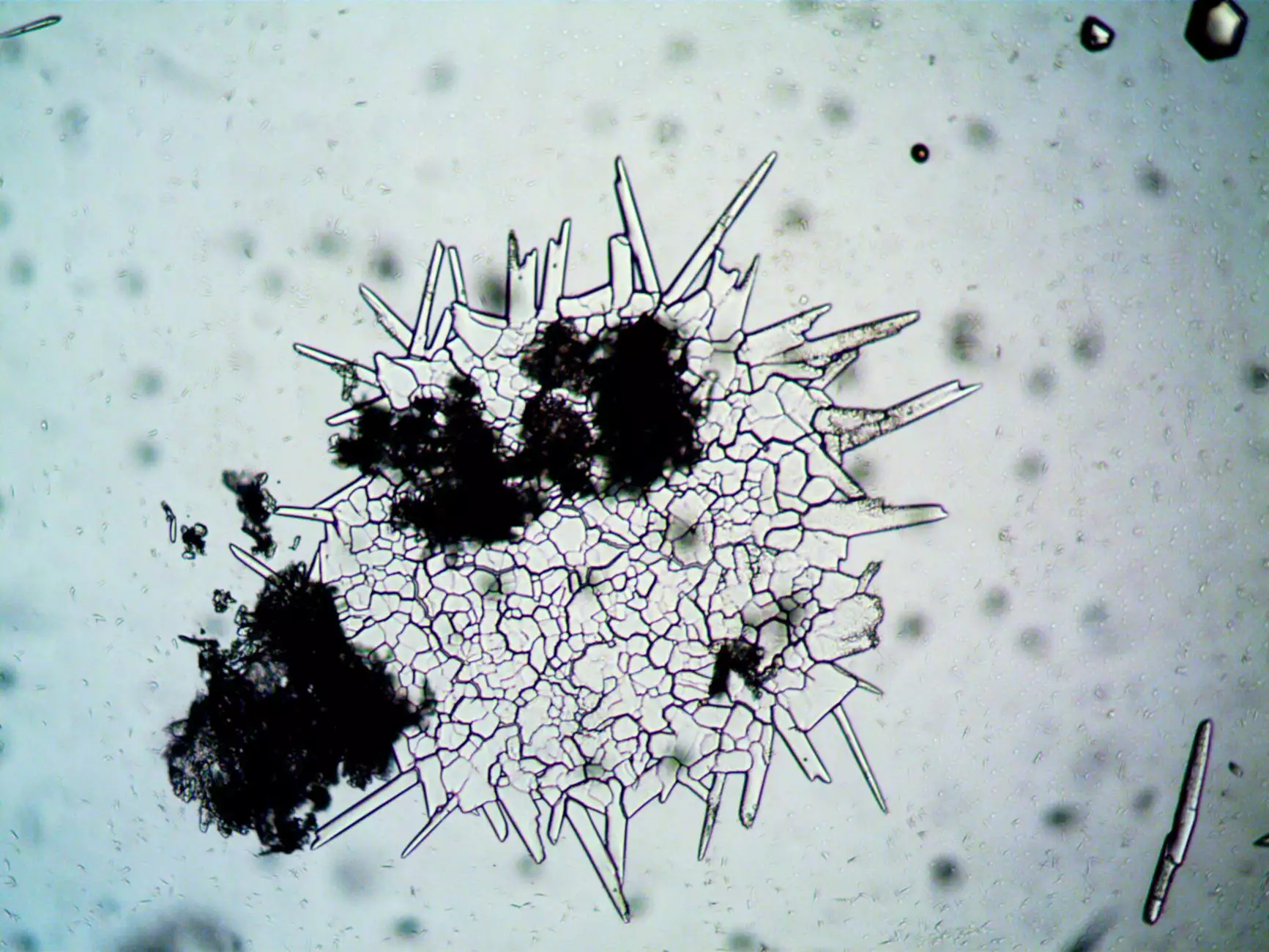
Understanding Injection Moulding
Injection moulding is a manufacturing process that produces parts by injecting molten material into a mould. The process is widely used for producing plastic components, but it has substantial applications in metal fabricators as well.
The Importance of Injection Moulding Tools
In the competitive landscape of manufacturing and fabrication, having the right injection moulding tools is crucial. These tools not only improve product quality but also enhance production efficiency. Let's delve into the various aspects of these essential tools.
1. Benefits of Using Injection Moulding Tools
Implementing advanced injection moulding tools in your manufacturing process comes with multiple benefits:
- High Precision: Due to the design of the injection process, parts can be manufactured with tight tolerances, ensuring that every piece meets the required specifications.
- Cost-Effective: While the initial investment in moulds can be high, the efficiency and speed of the injection process lead to lower per-unit costs in mass production.
- Versatility: With the ability to use a wide range of materials, including metals, plastics, and composites, moulding tools are adaptable to various industry needs.
- Reduced Waste: The process minimizes material waste compared to traditional fabrication methods, enhancing sustainability efforts.
- Fast Production: Parts can be manufactured rapidly, which is essential in meeting market demands and reducing lead times.
2. Applications of Injection Moulding in the Metal Industry
When discussing injection moulding tools, it is imperative to acknowledge their application within the metal industry:
- Custom Metal Parts: Moulding allows for the production of specialized components unique to specific applications in automotive, aerospace, and consumer goods.
- Prototype Development: Rapid prototyping using injection moulding tools can lead to faster product development cycles, allowing companies to stay ahead of competition.
- Mass Production: High-volume production runs benefit greatly from injection moulding due to its consistency and efficiency.
- Complex Designs: Injection moulding enables manufacturers to create intricate designs that would be difficult or impossible using traditional fabrication methods.
Choosing the Right Injection Moulding Tools
When selecting injection moulding tools for your business, consider the following attributes:
1. Material Compatibility
Different tools are designed to accommodate specific materials. Ensuring compatibility with the types of metals and plastics you plan to use is essential for optimal performance.
2. Tool Quality and Durability
Investing in high-quality tools may require a larger upfront capital, but the long-term savings and efficiency gained from their durability are worth it.
3. Technical Support and Service
A reputable supplier should offer ongoing support, maintenance, and training to help your team utilize the injection moulding tools effectively.
4. Cost Analysis
While an initial evaluation of costs is necessary, always consider the overall total cost of ownership, including maintenance, operation, and energy consumption.
Innovations in Injection Moulding Technology
The industry constantly evolves, with innovations that enhance the capabilities of injection moulding tools. Here are some of the latest advancements:
1. Automation and Robotics
Integrating robotics into the injection moulding process allows for greater automation, leading to reduced labor costs and fewer human errors.
2. Advanced Materials
New generations of materials are being developed that offer improved strength, lighter weight, and enhanced thermal properties, expanding the applications of injection moulding.
3. Energy Efficiency
Modern injection moulding tools are designed for energy efficiency, reducing the environmental footprint of manufacturing processes.
Best Practices for Using Injection Moulding Tools
To maximize the efficacy of your injection moulding tools, consider these best practices:
1. Regular Maintenance
Establish a routine maintenance schedule to ensure that your tools are always operating at peak efficiency and to prevent costly downtimes.
2. Training and Skill Development
Invest in training programs for your workforce to familiarize them with the operation and intricacies of the injection moulding process.
3. Process Optimization
Continuously analyze your production process and implement improvements to enhance quality and reduce cycle times.
Case Studies: Success with Injection Moulding Tools
1. Automotive Industry Applications
One of the leading automobile manufacturers reported a significant increase in productivity after integrating advanced injection moulding tools. By adopting high-precision moulds, they improved component fit and functionality while reducing scrap rates by over 30%.
2. Aerospace Innovations
A well-known aerospace company managed to cut down its production cycle time by 50% through effective use of injection moulding, utilizing lightweight yet durable materials for various components.
Conclusion: The Future of Injection Moulding in Metal Fabrication
As industries continue to progress, the role of injection moulding tools in metal fabrication becomes increasingly vital. Businesses that adopt these tools will not only enhance their operational efficiency but also position themselves strategically within competitive markets.
For businesses looking to improve their manufacturing processes, investing in quality injection moulding tools is not just an option—it's a necessity. At DeepMould.net, we are committed to providing state-of-the-art tools that elevate your business to new heights. Connect with us today to learn how we can assist you in transforming your manufacturing landscape.
Contact Us
If you're interested in learning more about how injection moulding tools can benefit your business, please visit DeepMould.net for more information.